Multi Cylinder Hydraulic Cone Crusher

High Crushing Ratio

High Productivity

Safety and Stability

High Comprehensive Benefit

Easy to Operate and Maintain

Good Granularity of Finished Product
Product Introduction
The multi cylinder hydraulic cone crusher is developed and manufactured by Talus Equipment Manufacturing incorporating foreign technology. It is suitable for crushing various ores and rocks with medium and above hardness, primarily used in secondary and tertiary crushing in the fields of metal mines and construction sand and stone. With its high rotational speed, large crushing capacity and special design, it insures excellent cubic product. The machine features a high-strength casting steel frame, an alloy material forged main axis, a high-precision straight bevel gear transmission structure and a multi-cavity selection and automated operation control system, which perfectly showcase its performance and advantages. This machine is available in standard and short head core types. Generally, the standard type has a larger feeding particle size and coarser discharge particle size, while the short head type has a steeper and smaller feeding size, making it suitable for producing fine-grained materials. Therefore, the standard type is generally used for coarse and medium crushing, while the short head type is used for medium and fine crushing.
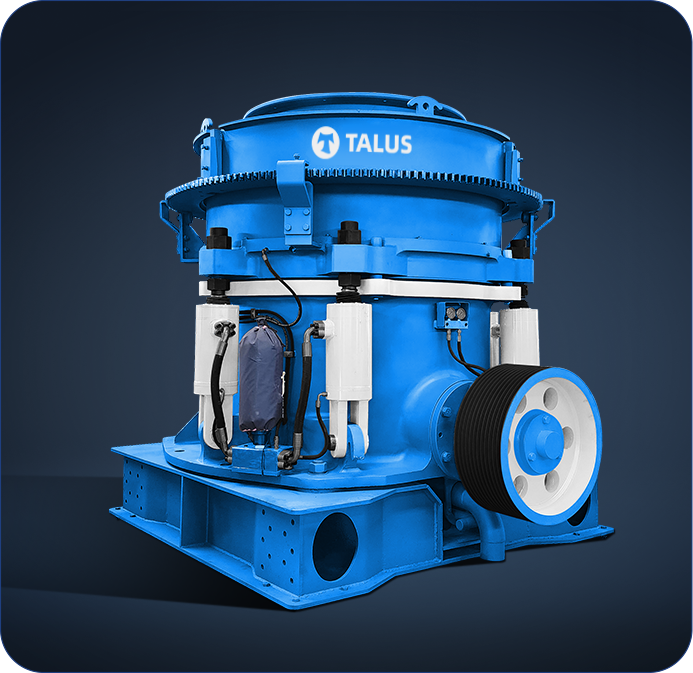
Product Performance

Inter-particle Crushing Design - Improved Discharge Granularity
The application of a large eccentricity (twice that of a single cylinder), high swing frequency, and inter-particle crushing principle results in a high capacity, large crushing ratio and good granularity.

Ingenious Liner Adjustment Method - Maximizing Liner Utilization
The hydraulic motor drives the adjustment sleeve (fixed cone liner) to accurately adjust the discharge port, ensuring stable feeding, high liner utilization and optimal granularity. The hydraulic motor also allows for turning the adjusting sleeve and the fixed cone liner turn out of the supporting sleeve to replace the fixed cone liner and the movable cone liner, greatly simplifying workload of liner replacement.

Easier Maintenance - Cost-Effective Operation
The advanced sealing method ensures a clean lubrication system, simplifies equipment maintenance, and provides convenient and quick part replacement.

Fixed Axis Design - Enhanced Bearing Capacity
Fixed axis design boasts high main axis strength, capable of withstanding greater crushing force.

Advanced Hydraulic Protection Device - Increased Automation
The bidirectional tramp releasing hydraulic cylinder allows iron blocks to pass through crushing cavity smoothly, ensuring excellent iron detection performance continuous operation of equipment and high production efficiency. Hydraulic cavity cleaning function easily and quickly removes accumulated materials in the crushing cavity, greatly reducing labor intensity and improving work efficiency.

Overall Steel Frame Structure Design - Stable Operation
The overall steel frame structure design simplifies on-site foundation production and allows for quick installation. The standard configuration of six-piece rubber spring supports throughout the entire series ensures stable equipment operation while minimizing impact on the foundation.
Operation Principle
The movable core of crushers performs a rotary swing motion driven by the action of eccentric sleeve. This motion drives the mantles to squeeze and rub the material between the mantle and concave surface. According to inter-particles crushing theory, the material is subjected to forces from multiple directions, resulting in crushing and polishing that aligns with its own texture. Consequently, stable particles are formed. Particles that meet the discharge requirements are released from the swing gap between the mantles, while the remaining materials undergo continuous crushing until the desired particle size is achieved.
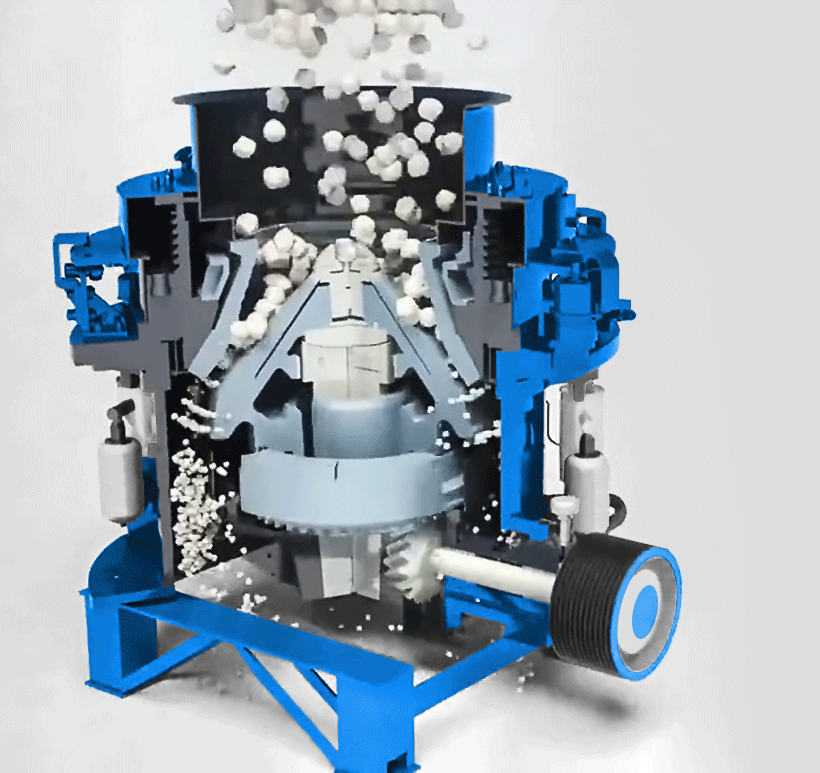
Technical Parameter
Remark: The output may vary depending on the nature or grain size of the feeding material.
Model | Cavity | Diameter of bottom end of conical crushing head (mm) | Feeding opening size (mm) | Max. feeding size (mm) | Nominal capacity in t/h with crusher running at CSS (mm) | Crushing capacity (t/h) | Motor power (kW) | Host weight (t) |
---|---|---|---|---|---|---|---|---|
HPM200 | C1 | 900 | 185 | 145 | 22 | 160~250 | 160 | 11 |
C2 | 125 | 100 | 18 | 145~250 | ||||
C3 | 95 | 75 | 14 | 120~250 | ||||
F1 | 76 | 60 | 12 | 108~210 | ||||
F2 | 54 | 45 | 10 | 81~210 | ||||
HPM300 | C1 | 1100 | 235 | 190 | 26 | 230~445 | 220 | 20 |
C2 | 211 | 170 | 20 | 200~445 | ||||
C3 | 150 | 120 | 16 | 180~445 | ||||
C4 | 107 | 85 | 14 | 160~220 | ||||
F1 | 53 | 40 | 12 | 140~220 | ||||
HPM400 | C1 | 1400 | 299 | 240 | 35 | 270~630 | 315 | 27 |
C2 | 252 | 200 | 25 | 252~630 | ||||
C3 | 198 | 160 | 25 | 243~630 | ||||
C4 | 111 | 190 | 18 | 210~630 | ||||
F1 | 92 | 75 | 15 | 162~370 | ||||
F2 | 52 | 40 | 13 | 126~370 | ||||
HPM500 | C1 | 1500 | 335 | 270 | 38 | 365~790 | 400 | 40 |
C2 | 286 | 230 | 30 | 328~790 | ||||
C3 | 204 | 165 | 22 | 280~790 | ||||
C4 | 133 | 105 | 20 | 202~450 | ||||
F1 | 95 | 75 | 16 | 175~450 | ||||
F2 | 52 | 42 | 8 | 158~450 | ||||
HPM650 | C1 | 328 | 262 | 30 | 386~790 | 500 | ||
C2 | 279 | 225 | 25 | 348~790 | ||||
C3 | 196 | 175 | 20 | 300~790 | ||||
F1 | 106 | 85 | 13 | 280~530 | ||||
F2 | 52 | 42 | 9 | 220~530 | ||||
HPM800 | C1 | 2000 | 353 | 280 | 38 | 616~1100 | 630 | 70 |
C2 | 297 | 240 | 38 | 522~1100 | ||||
C3 | 267 | 214 | 25 | 495~1100 | ||||
C4 | 219 | 175 | 22 | 380~1100 | ||||
F1 | 155 | 125 | 20 | 328~730 | ||||
F2 | 92 | 75 | 16 | 270~730 |
Product Structure
From exterior design to internal structure, every detail has been meticulously considered and thoroughly tested.
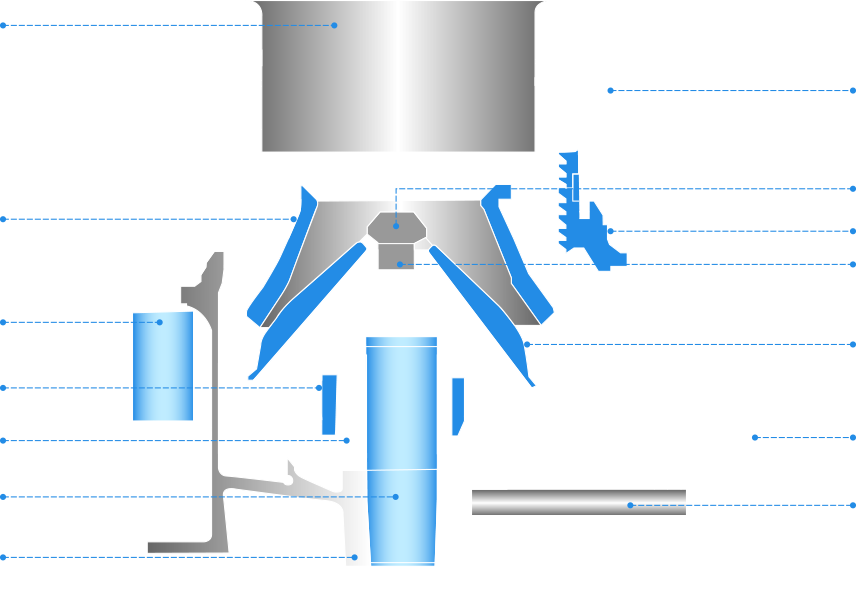
Product Show
From exterior design to internal structure, every detail has been meticulously considered and thoroughly tested.
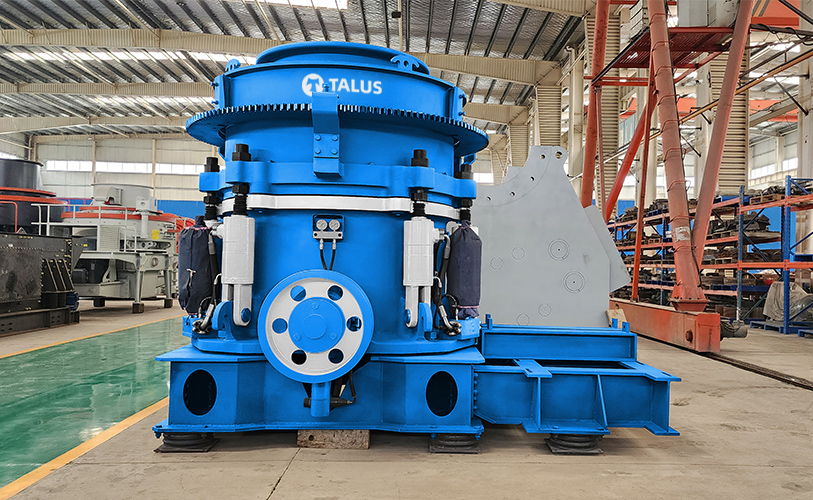
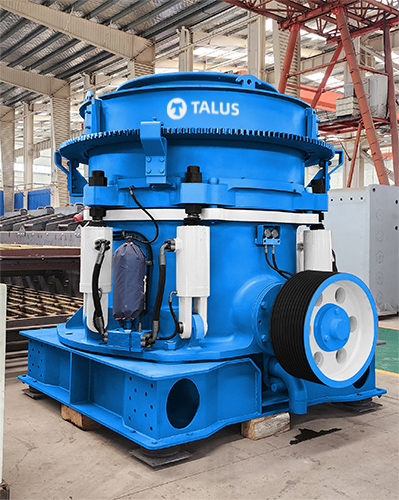
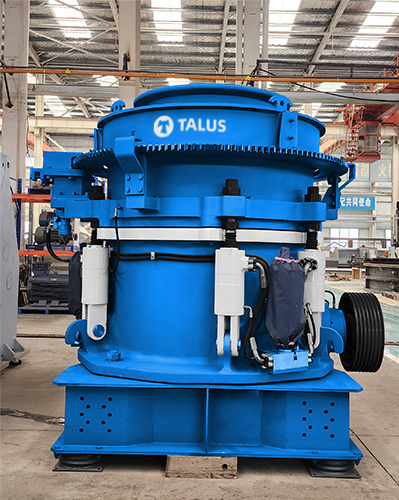
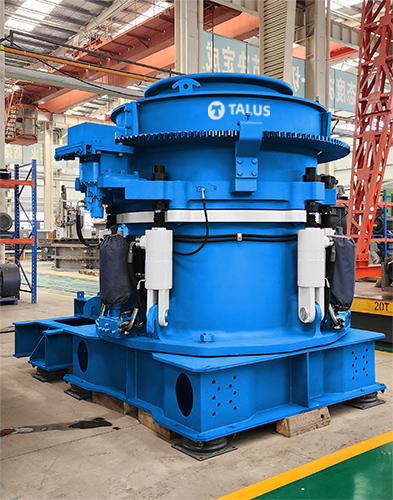
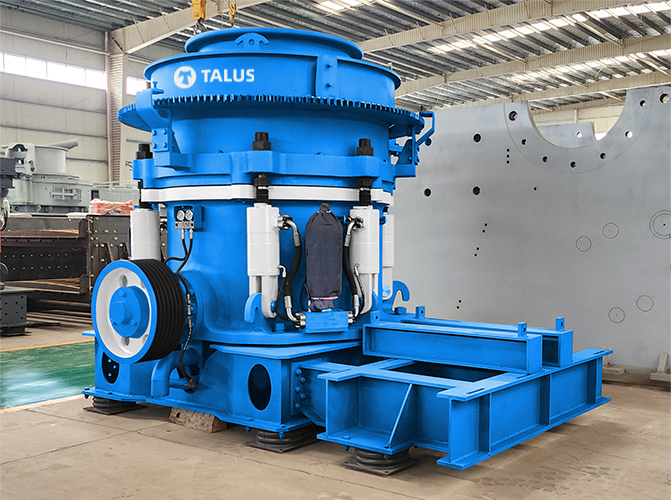
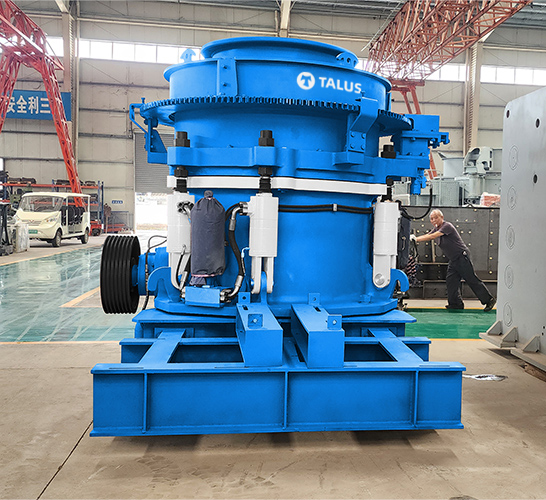
More Device Recommendation
Perhaps you are still in need of further device recommendations
CLV Vertical Shaft Impact Sand Making Machine
PFL Vertical Compound Sand Making Machine
Talus Sand Making Machine
CH Single Cylinder Hydraulic Cone Crusher
Please kindly submit your request for a comprehensive product offer